Case Study
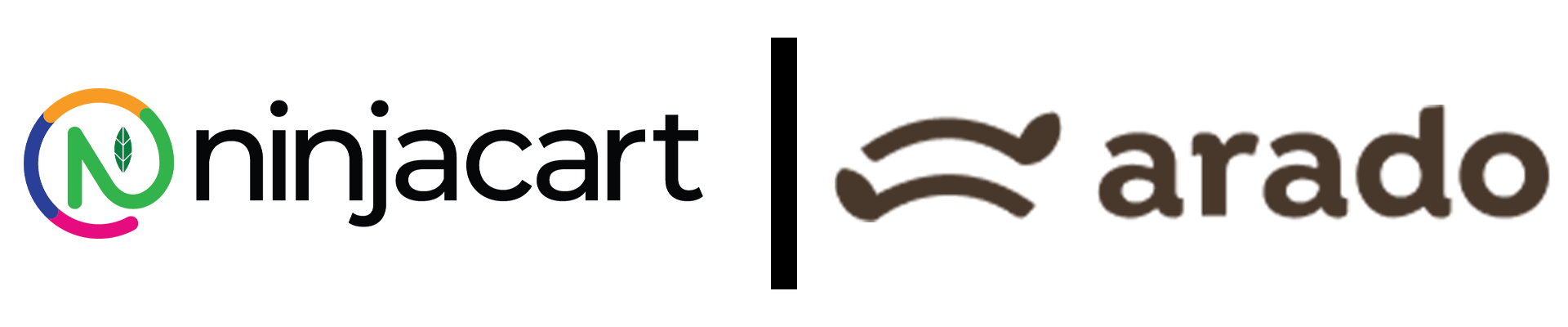
Inventory & Operations

Problem Statement

Arado, a fresh-produce delivery startup was looking for upgradation and modernization of their
existing Supply chain operations in their home region of Brazil. As part of this endeavor, Ninjacart
decided to implement its Inventory and Operations Management solution in Arado’s ecosystem to
help fulfil this requirement. The key Business drivers for this project were identified as:
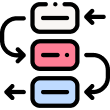
Effectively track and move the inventory across the Supply chain zones
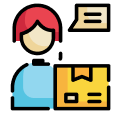
Define logics for transforming stock into Customer orders
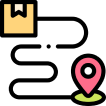
Design process workflows that best-fit a time sensitive order delivery window
Solution Approach

A four-point solution approach was undertaken for this project:
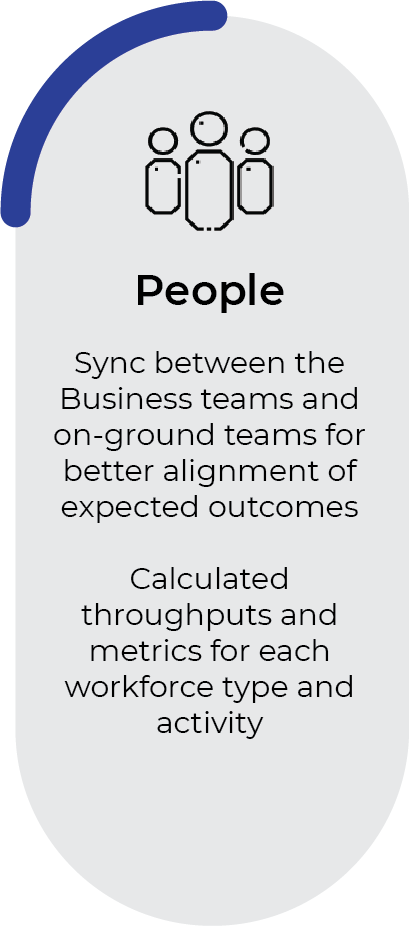
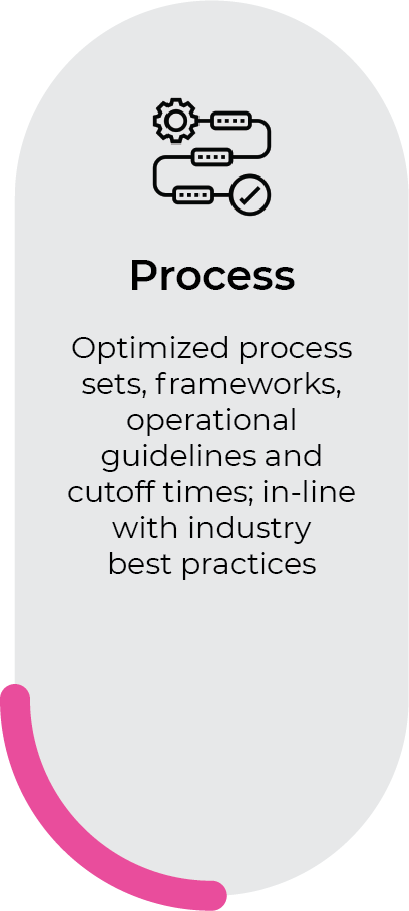
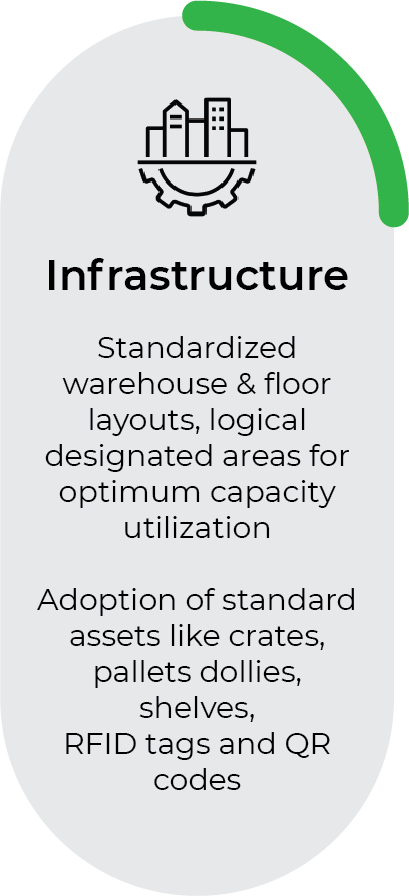
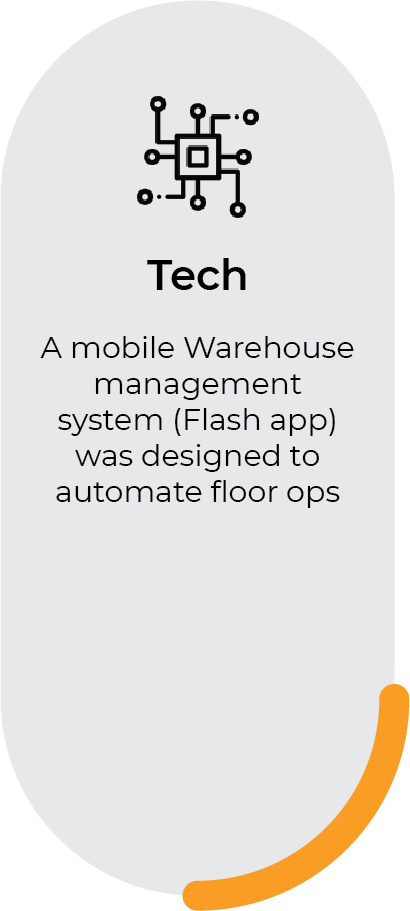
Engagement Model


Flash app, which is used by the on-ground operations team to:
- Manage and handle the stock receiving from Farmers, vendors or Interfacility
- Execute the instructional workflows for activities such as Batching, Lotting, Picking, Loading and Dispatch

Bifrost (Central ERP), which is used by the Central teams to:
- Monitor the on-ground team performance and adherence to cut-off times
- Manage the demand & supply linkage i.e., Pick-n-Run generation
- Get instant stock counts & availability and track profitability
- Take corrective actions to tackle any onground problems faced
Outcome

Arado now operates in an asset light and paperless model of immaculate planning
and on-ground execution
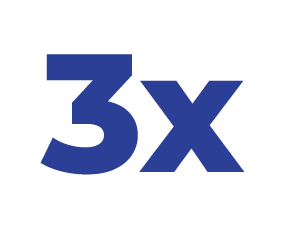
increase in warehouse capacity (daily tonnage)
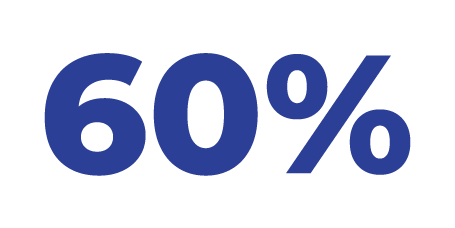
reduction in Inventory errors (processing)
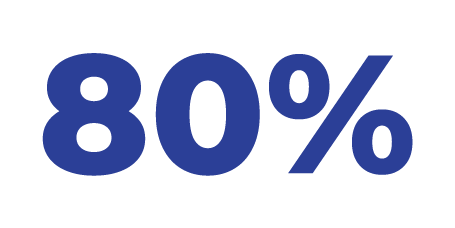
reduction in losses (pilferage)
Testimonials

“Using Ninjacart’s Inventory and Warehouse Management solution, we have significantly streamlined our operations. Their automated workflows with RFID tagging have provided us with better control over our assets and stock, reducing loss and pilferage. The real-time traceability feature has helped us build a scalable supply chain model that suits our business in Brazil. Within six months of deployment, we are already seeing significant improvement in the inventory inward and receiving process at the distribution center. The system-based instructions help guarantee that the standard processes are followed.”
Isabella Genova
Project Manager at Arado
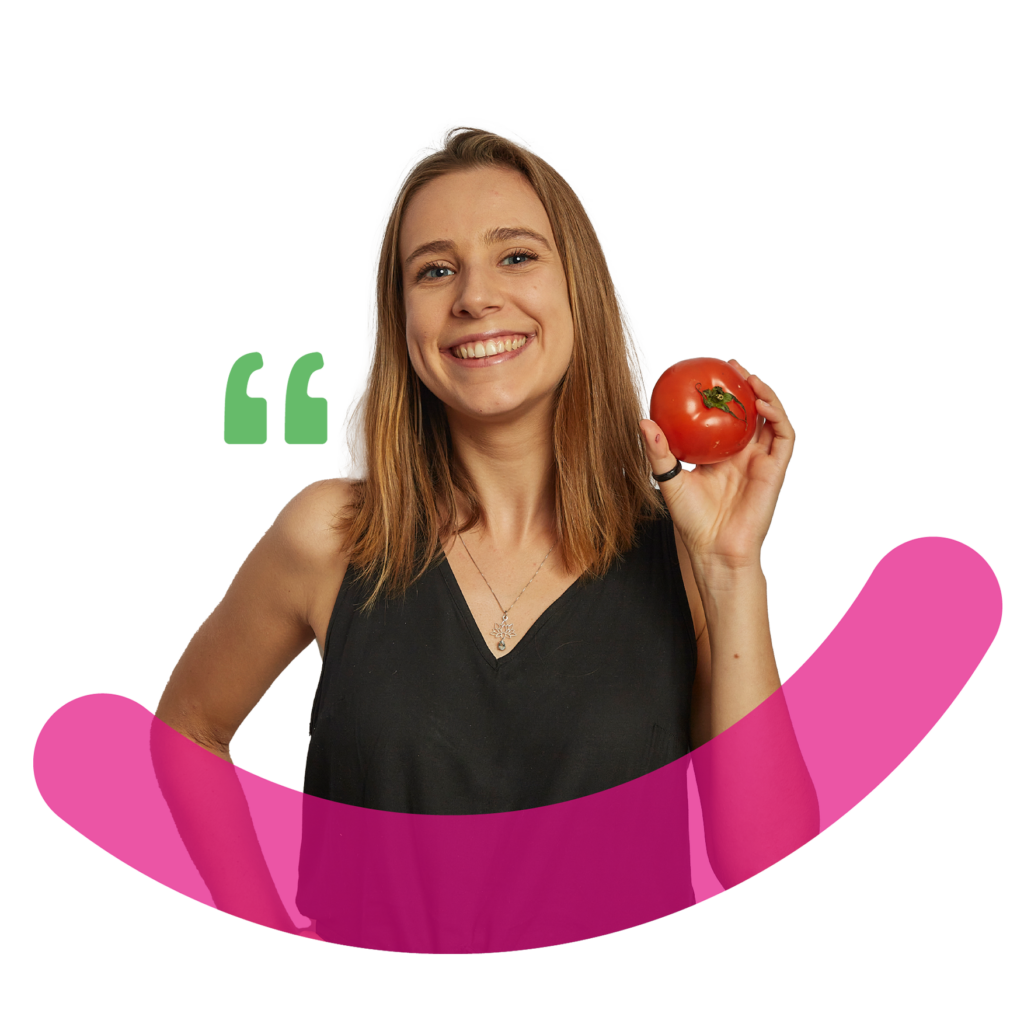
“Our Business and Operations have greatly benefited from Ninjacart’s Inventory Management solution. With real time traceability we now have an accurate, centralized view of our demand-supply linkage, inventory and order fulfilment status. Moreover, the solution by perfectly adapting to our business needs, has helped us optimize our warehouse layouts, standardize assets & process workflows and improve workforce productivity. Today we are able to avoid manual errors and foster efficiency with a system-based instructional approach that is enabled through the mobile WMS”
Bruno Mengatti
Chief Operating Officer at Arado
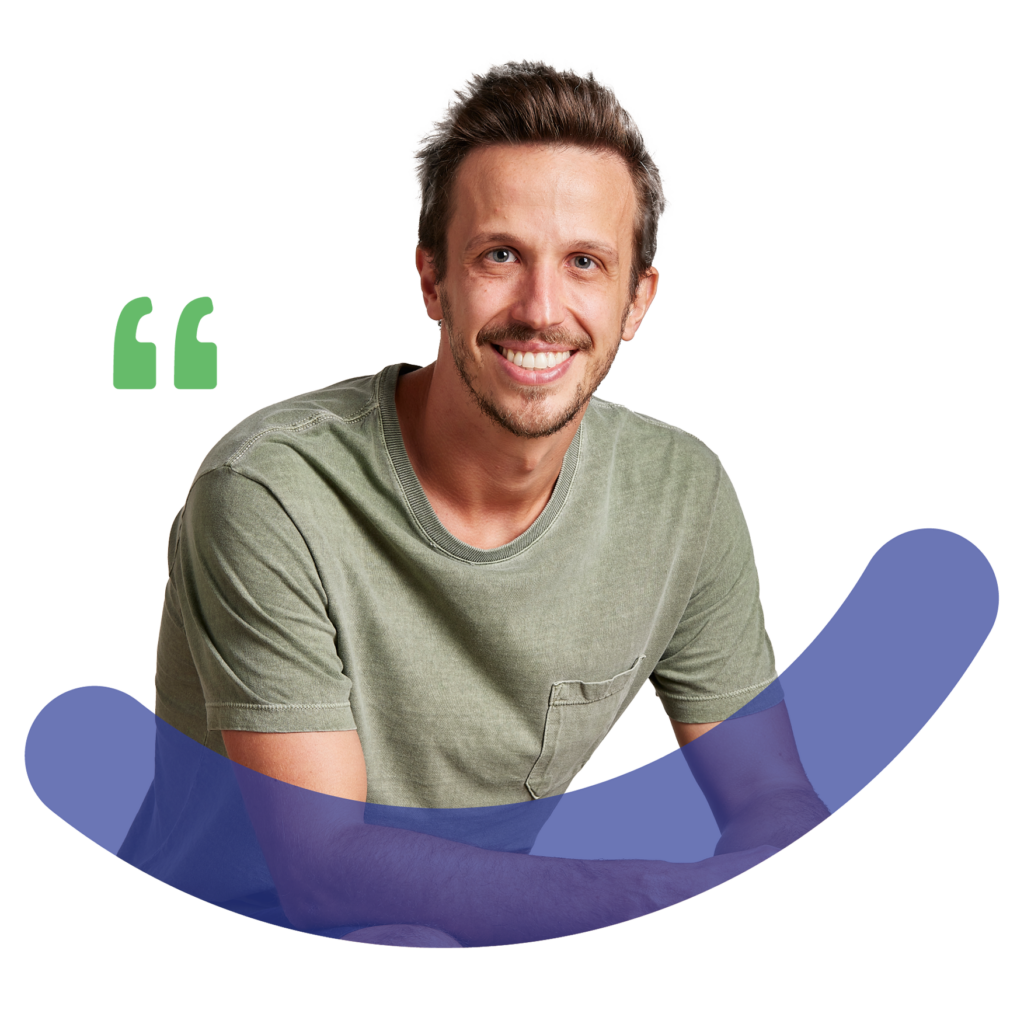
“Ninjacart has helped us automate our Inventory and Order management processes. Their RFID enabled workflows have enabled us to gain better control over our assets and stock with a centralized monitoring framework, reducing loss and pilferage. The system-based instructions significantly reduce the manual errors (up to 60-70%) and their mobile WMS system lessens the need for workforce training and onboarding overheads”
Victor Bernardino
Chief Executive Officer at Arado
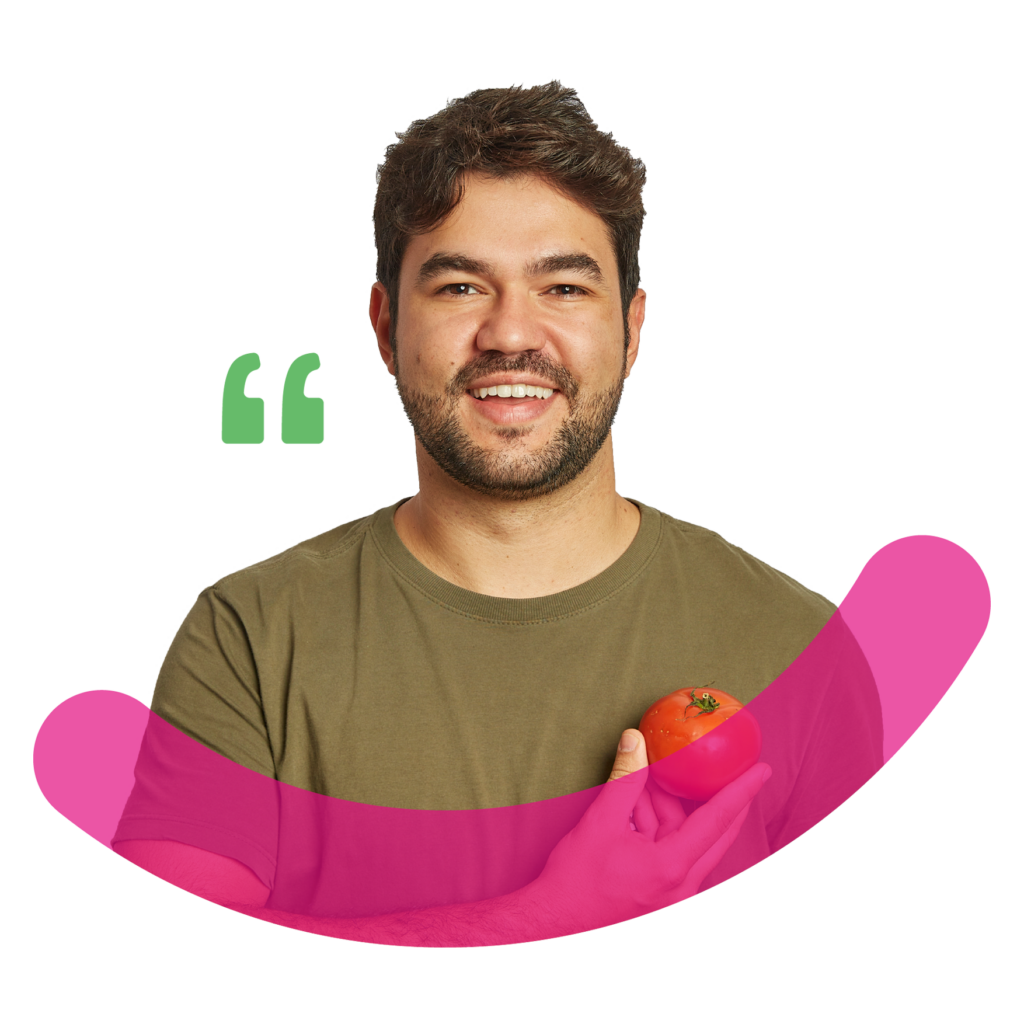
Our Journey

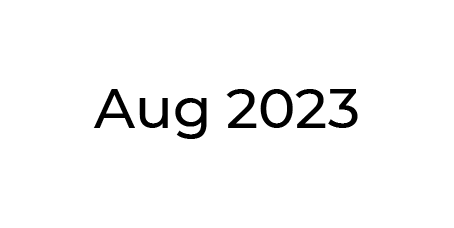
Project Kick-off
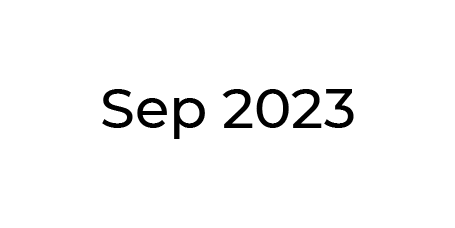
Discovery and BRD Sign off
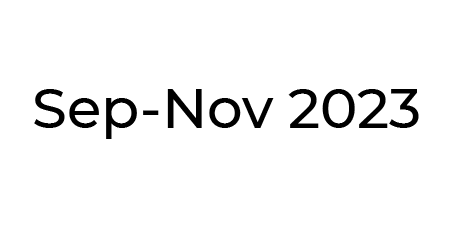
Tech Development, Infra readiness and UAT
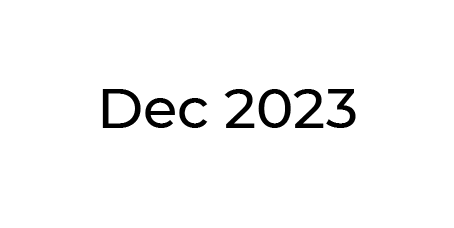
First module Go-Live
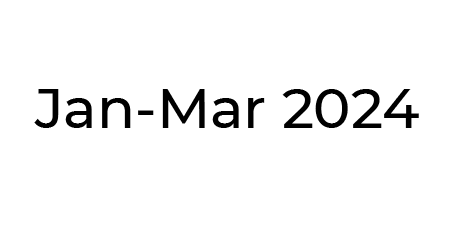
Support and Handover
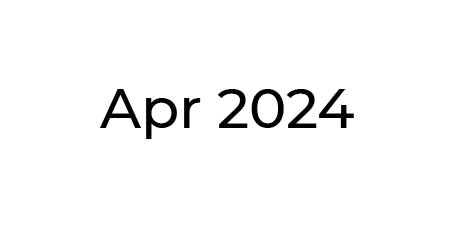
Expansion in other cities
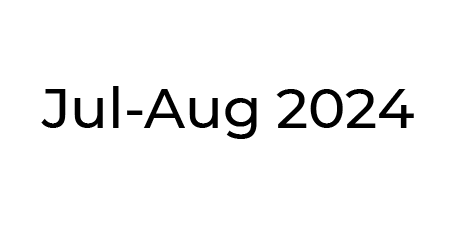
Development of Last module to (E2E) Go-Live
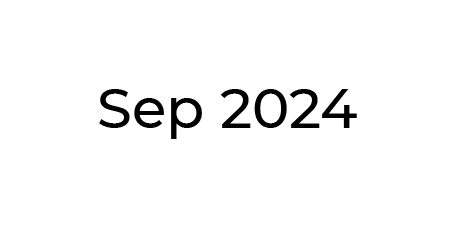
Final Go-Live
To learn more about the Ninja Tech Ventures solutions featured in this story, please contact your Ninja Tech Ventures representative or reach out to us at partnerships@ninjacart.com